Maintenance of electric drill
Release time:
Apr 20,2023
Due to the need for ventilation and heat dissipation, the electric drill has a lot of dust inside for a long time. The dust will cause the lubricating oil on the gear and bearing (sliding sleeve) to be mixed, deteriorated, absorbed and aggravated by wear, especially for alternative use. In order to ensure the rotation accuracy of the electric drill and reduce the excessive clearance caused by the wear of the bearing (sliding sleeve), it is extremely necessary to keep the internal clean and greased lubrication.

Due to the need for ventilation and heat dissipation, the electric drill has a lot of dust inside for a long time. The dust will cause the lubricating oil on the gear and bearing (sliding sleeve) to be mixed, deteriorated, absorbed and aggravated by wear, especially for alternative use. In order to ensure the rotation accuracy of the electric drill and reduce the excessive clearance caused by the wear of the bearing (sliding sleeve), it is extremely necessary to keep the internal clean and greased lubrication.
Methods:
Loosen several self-tapping nails or screws outside the electric drill; Lay flat and open half of the shell; Generally, the structure of the new hand electric drill is semi-embedded, that is, all the machine and electrical components are mounted in the other half of the shell.
Carefully remove the carbon brush first, then the end of the drill chuck, then gently lift the motor to take out the rotor (do not damage the enameled wire), clean the commutator on the rotor (the one in contact with the carbon brush), if it is too dirty or severely worn, polish it with emery cloth first and then with water sandpaper or metallographic sandpaper until it is bright.
If the bearings before and after the rotor are sealed, the outside can be wiped clean. If the seal is broken, replace it in time. Clean the screw tooth shaft in front of the rotor
Clean the oil stains inside the shell. Clean the helical gear on the drill chuck rod and the bearings (or shaft sleeves) at both ends.
Put the removed parts back, first install the rotor; then install the helical gear of the drill chuck rod; install the carbon brush. If the carbon brush is shorter than 7-8mm, replace it with a new one in time. The carbon brush should be installed and flattened. Find a little "Mobil" or "Shell" grease to add between the gear pair and the bearing (or shaft sleeve). All parts should be installed and flattened. After checking that the other half is correct, the other half can be covered. Tighten the screw and turn it by hand without jamming before it can be powered on and tested.
Previous Page
Recommended News
Classification of electric hammer
Oct 13,2023
Common faults of electric hammer
Oct 08,2023
Application of electric hammer
Sep 25,2023
Electric hammer maintenance method
Sep 22,2023
Thanos-subvert tradition, refresh strength
Sep 09,2023
Domestic excellent professional lithium battery tool manufacturer
Address: Tianfen Industrial Park, Qidong City, Jiangsu Province, China.
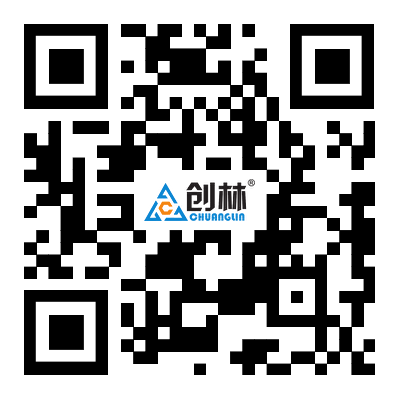
View mobile version
Copyright © 2023 YINXIANG Electromechanical Business License